…maar weten we wat we meten?
Eén handeling die tijdens een inspectie, die conform de ISO 17020:2012 wordt uitgevoerd, vaak wordt onderschat is een meting. Een meting correct uitvoeren en een betrouwbaar meetresultaat verkrijgen kan als uitdaging van het inspectievak gezien worden.
Inspectieschema’s proberen vaak om metingen als ‘niet-kritisch’ aan te merken om te ontkomen aan de verplichting voor inspectie-instellingen van kalibratie en herleidbaarheid. Op basis van RvA T018 worden metingen dan, vaak zonder geldige onderbouwing, in de categorie B ingedeeld. Kalibratie van meetinstrumenten is daarmee voorkomen, maar de meting is daarmee gelijktijdig gedegradeerd tot een overbodige handeling. Immers, als je niet weet wat je meet, meet je feitelijk helemaal niets.
Naast kalibratie van een meetinstrument zijn er nog veel meer factoren die het resultaat van een meting beïnvloeden. Deze factoren zijn hieronder in de Ishikawadiagram weergegeven:
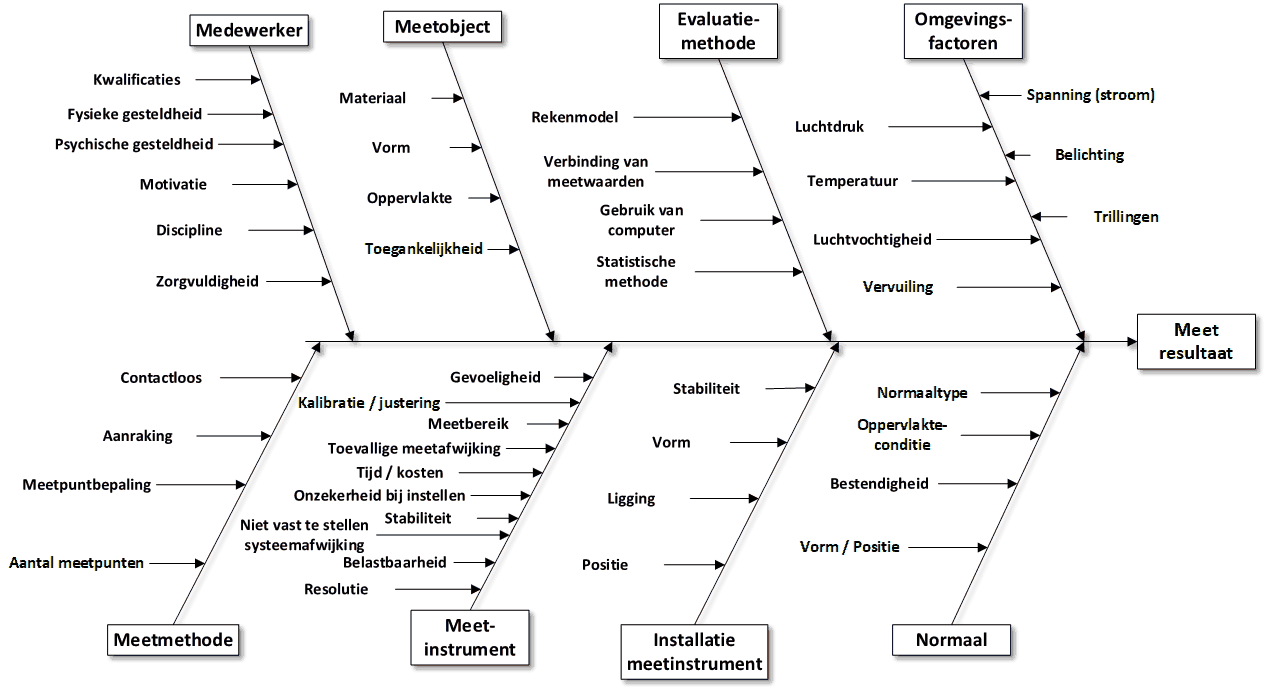
De moeilijkheid zit hem in de veelvoud aan factoren die van invloed zijn op een meting, zoals: de meetmethode, het meetmiddel en weliswaar de gevoeligheid en de tijd die voor een meting benodigd is, de kalibratie, de toevallige afwijking, de niet geregistreerde systematische afwijking, een onzekerheid bij het afstellen, voorts die positie waar de meting plaatsvindt (de stabiliteit, de ligging, de positie), de “normale” gegevens (bijvoorbeeld oppervlakte eigenschap, en consistentie van de meting etc.), verder speelt de omgeving een rol: luchtdruk, temperatuur, luchtvochtigheid, vervuiling, spanning (bij elektriciteit) belichting en trillingen. Een meting wordt ook geëvalueerd (uitgelezen) en meetwaarden worden met elkaar in verband gezet. Het meetobject, te weten het materiaal, het oppervlak, de vorm en de toegankelijkheid en last but not least de inspecteur, die de meting uitvoert: de kwalificatie, ervaring, psychische en fysieke conditie, de zorgvuldigheid, de discipline en motivatie dienen meegewogen te worden.
Toleranties en meetonzekerheden dienen berekend te worden en in het meetsysteem en in het meetproces te worden meegenomen. Voor de bepaling van de meetonzekerheid kan, indien deze bijvoorbeeld door uitgevoerde kalibraties bekend is de MPE (Maximum Permissible Error) gehanteerd worden.
Met deze kennis wordt direct duidelijk, dat de kans groot is dat 10 verschillende inspecteurs ook 10 verschillende meetresultaten opleveren bij hetzelfde meetobject. Het is aan de inspectie-instelling om deze verschillen binnen acceptabele grenzen te brengen en te houden. Een goede vastlegging van de meetmethode, het kalibreren van meetinstrumenten en het toezien op de juiste uitvoering van de methode en het juiste gebruik van de instrumenten is daarom van belang.
Kleine tip voor diegene die niet weten waar ze moeten beginnen: In het begin van een opzet van een meting dient altijd als eerste vastgesteld te worden of het beoogde meetproces geschikt is. Vervolgens wordt beoordeeld of het meetproces, rekening houdend met de minimale tolerantie, nog steeds geschikt is. Daarna worden de overige aspecten bekeken.
Een uitkomst bieden ook deze twee ISO-normen:
- ISO 14253-1:2017 Geometrical product specifications (GPS) – Inspection by measurement of workpieces and measuring equipment – Part 1: Decision rules for verifying conformity or nonconformity with specifications; Nederlandse titel: Geometrische productspecificaties (GPS) – Keuring door meting van werkstukken en meetapparatuur – Deel 1: Beslissingsregels voor het aantonen van overeenstemming of niet-overeenstemming met de specificaties
- ISO 22514-7:2012 Statistical methods in proces management –Capability and performance Part 7: Capability of measurement processes; Nederlandse titel: Statistische methoden in procesmanagement – Vermogen en prestatie – Deel 7: Vermogen van meetprocessen.